民用碳纤维降本是核心。
碳纤维以“价格”换“需求”,在保持企业合理利润水平下,为使碳纤维性价比快速提升,降本成为核心。对企业来讲,竞争力的体现集中在成本端。而从降本的方式来看,主要有两个方向,一是通过发挥规模效应,降低吨折旧/吨能耗;二是通过优化流程/提升技术,提高效率。
产能规模/产品结构不同导致吨成本差异较大。
从行业历史吨成本来看,整体呈现下降趋势。受规模效应影响,不同规模的碳纤维企业吨成本有所差异。其中,中简科技/光威复材吨成本较高,也由于中简科技/光威复材产品结构中军品占比较高;吉林碳谷吨成本较低,也由于吉林碳谷产品主要为碳纤维原丝。
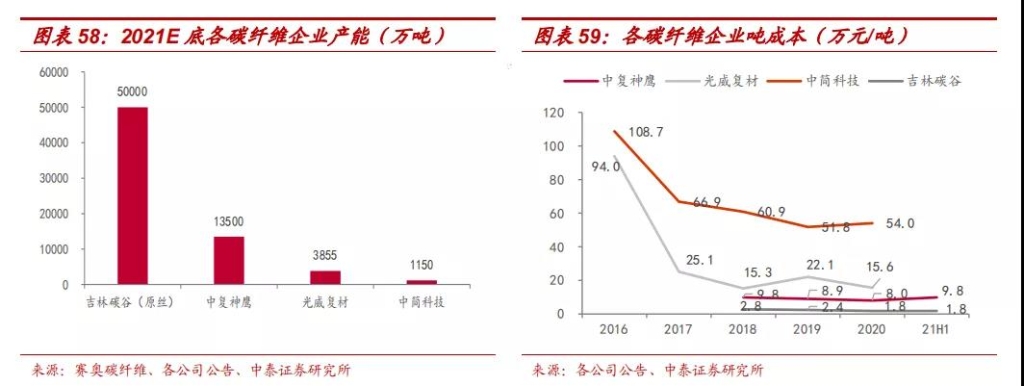
产业链中不同环节成本构成差异较大,碳丝生产环节存在规模效应。
由于处于产业链中不同环节,各企业间成本构成略有差异。中复神鹰/光威复材/中简科技包含原丝及碳丝生产环节,在成本构成中,制造费用占比偏高(固定成本高/能耗高),2020 年分别占比 57.5%/64.6%/76.2%。而吉林碳谷仅包含原丝生产环节,直接材料占比较高,2020 年占比达到61.0%,制造费用及能耗占比相对而言并不高,2020 年合计占比为35.6%。碳纤维生产中制造费用占比高,反映出碳纤维生产的固定成本高/能耗量大,因此制造费用部分存在更为明显的规模效应(直接材料和人工也存在规模效应)。随着技术进步/产能规模扩张/产能利用率提升,固定成本摊薄更多,能源使用效率提升,整体生产成本有望下降。
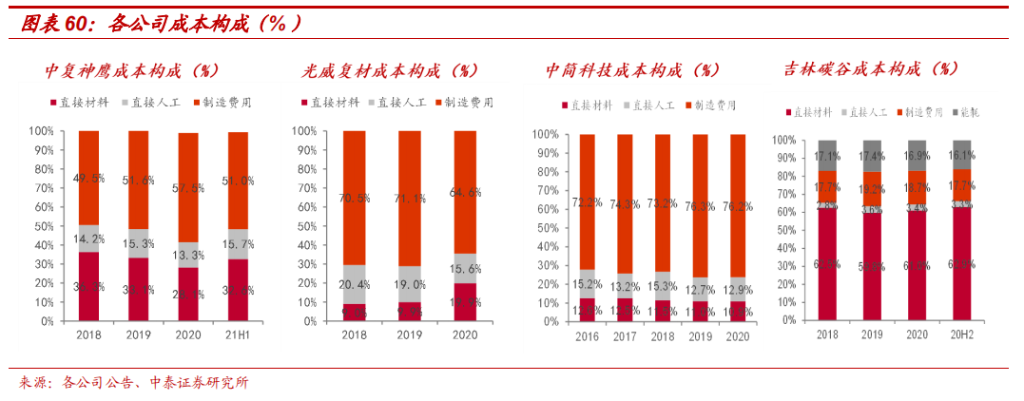
吨折旧/吨电费为取得成本优势的主要切入点。
在制造费用中,2020 年中复神鹰折旧/电费分别占比 23.8%/32.6%,2018 年中简科技折旧/电费分别占比 41.7%/30.2%,因此吨电耗/吨折旧成为取得成本优势的主要切入点。由于产品结构不同,2018 年中简科技吨电耗为 24.37 万度,2020年中复神鹰吨电耗为 2.85 万度。原丝生产环节耗电量较少,21H1 吉林碳谷吨电耗为 0.17 万度。
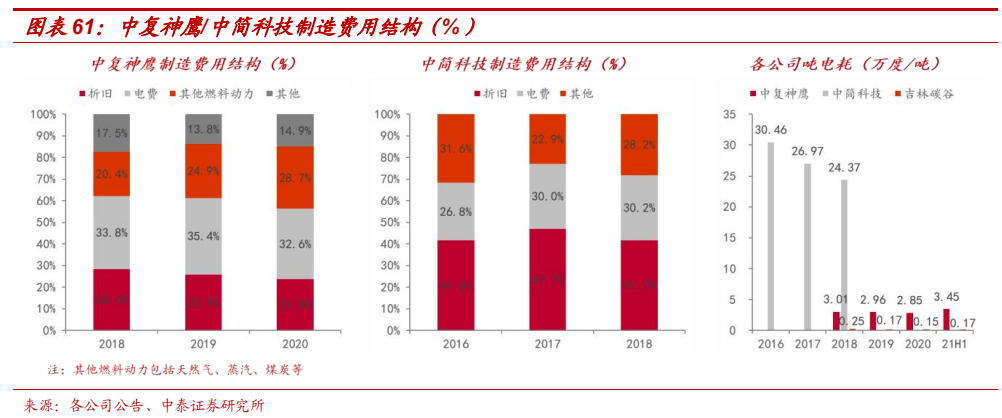
碳纤维生产规模化可以有效地降低生产成本。
根据《PAN 基碳纤维生产成本分析及控制措施》,随着生产规模、产量的增加,非直接生产因素占总成本的比例逐渐减小,大规模原丝(3000t/a)和碳纤维(1000t/a)直接生产费用分别是小规模原丝(250t/a)和碳纤维(100t/a)直接生产费用的 60.94%和 48.34%。根据《碳纤维产业化发展及成本分析》统计,原丝和碳纤维的产能和生产成本呈反比关系,千吨级碳纤维产线每年成本较百吨级产线下降 18%。
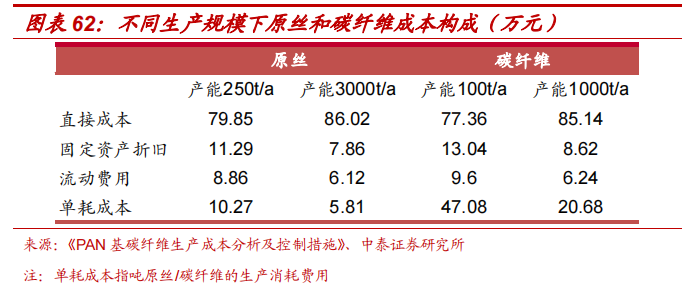
原材料丙烯腈吨消耗量仍有下降空间。丙烯腈为主要原材料,根据中复神鹰公告,21H1 中复神鹰原材料成本构成中,丙烯腈占比约 74%,其他原材料(包括二甲基亚砜、助剂和水性环氧树脂等)占比约 26%。根据中复神鹰公告,每吨碳纤维理论耗用丙烯腈 1.96 吨,21H1 中复神鹰吨丙烯腈消耗量为 2.06 吨(其中本部吨消耗量 1.96 吨,接近理论值,西宁产线处于投产初期吨消耗量 2.53 吨)。受原丝质量/碳化工艺等原因影响,国内并非所有企业均可达到吨丙烯腈消耗量为 1.96 吨的理论值,如 2018 年中简科技吨丙烯腈消耗量虽降至 2.26 吨,但相较理论消耗量仍略有差距。随着技术的进步以及技术外溢,行业整体吨丙烯腈消耗量仍有下降空间。

从生产工艺方面,可通过优化纺丝工序/氧化炭化工序实现效率的提升。
在纺丝工艺方面,由于湿法纺丝的纺丝速度小于
100m/min
,而在相同
条件下,干喷湿纺的纺丝速度可以提高到
300m/min
,根据《
PAN
基碳
纤维生产成本分析及控制措施》,若采用干喷湿纺工艺,同样的纺丝装备
及能源消耗条件下,产量提高
2-8
倍,
PAN
基碳纤维原丝的生产成本可
降低
75%
。随着干喷湿法工序的推广,行业生产效率有望进一步提升。
在氧化炭化工序方面,根据《
PAN
基碳纤维生产成本分析及控制措施》,
可通过液态化加热技术缩短预氧化反应时间,使碳纤维生产效率提高
50%
以上。在碳纤维表面处理过程中,由传统的热风非接触式干燥方式改为
蒸汽、热油等热辊接触式干燥方式,干燥时间和能耗均降低约
2/3
。
文章来源 | 中泰证券
孙 颖,聂 磊,朱晋潇
全文详见文章原文